Atomo ensures the efficient use of materials, energy, and resources by implementing programs focused on reducing plastic use and costs, while continuously striving to enhance environmental and sustainability performance.
Manufacturing Capabilities
Atomo's facility is based in Cape Town, South Africa, and is equipped with fully validated and verified processes and equipment, ensuring high standards in manufacturing. The site has been audited by the World Health Organization (WHO), the Therapeutic Goods Administration (TGA), SAHPRA (South African Health Product Regulatory Authority and the British Standards Institution (BSI) under ISO 13485:2016.
Atomo offers a flexible manufacturing process with the option to produce a wide range of batch sizes, including smaller batches for sample evaluation and other testing requirements during product development. The current facility capacity can support up to 3 million units which include test strip production and secondary packaging, and has the capability to expand to more than 10 million units per year.
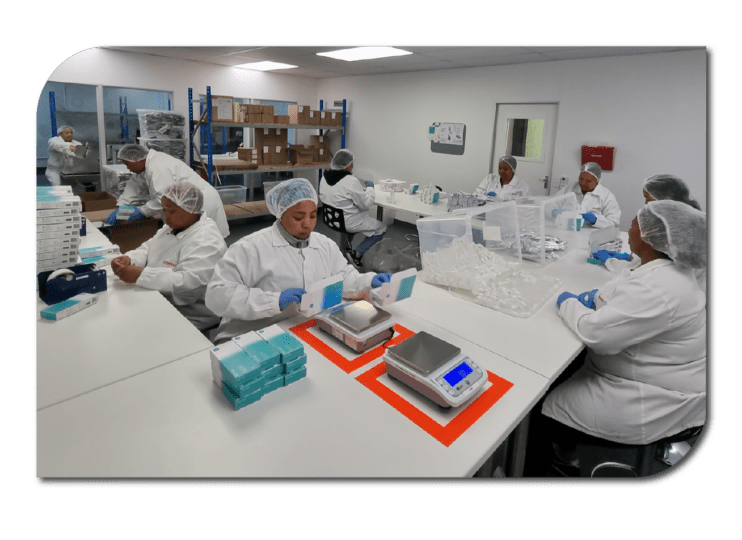
Global Health Focus
There is a growing push to increase procurement of HIV-related commodities from Africa. Currently, PEPFAR (The U.S. President’s Emergency Plan for AIDS Relief) procures less than 1 percent of the value of these commodities from the continent, largely due to the limited number of high-volume HIV product manufacturers in Africa. However, with rising demand, especially for HIV self-testing, there is a significant opportunity for growth. According to UNITAID, the demand for HIV self-testing is expected to reach nearly 30 million tests per year by 2025.
In response to this growing need, PEPFAR has set an ambitious goal to procure 15 million HIV tests from African manufacturers by 2025. Atomo, a leader in this space, currently provides the only prequalified HIV self-test manufactured in Africa. With a state-of-the-art manufacturing facility in South Africa, Atomo is well-positioned to meet this increasing demand and is planning to expand its capacity accordingly.
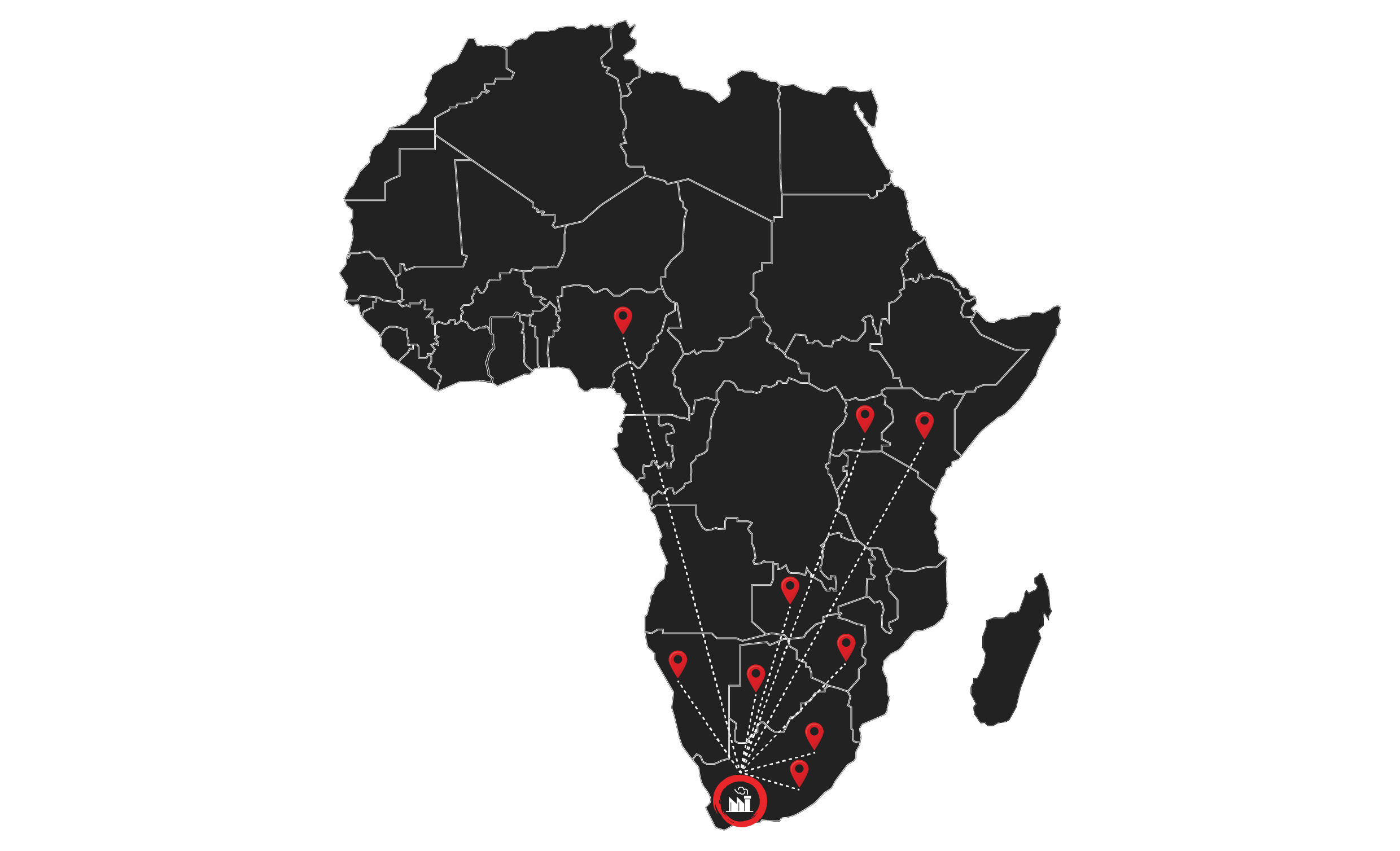
The Mylan HIV Self Test, manufactured by Atomo Diagnostics in our Cape Town facility, is distributed from South Africa to Lesotho, Namibia, Botswana, Zimbabwe, Zambia, Nigeria, Kenya and Uganda
The local production of diagnostic products in Africa offers numerous benefits, including supporting local jobs, facilitating skills transfer, and reducing logistics costs and the environmental footprint associated with the supply of tests into Africa. Atomo’s involvement in this growing sector is further highlighted by its participation as a panellist in the rapid diagnostic manufacturing consultation organised by PEPFAR. This engagement reflects Atomo’s commitment to advancing local production and meeting the rising demand for HIV testing across the continent.
Atomo's Advantage
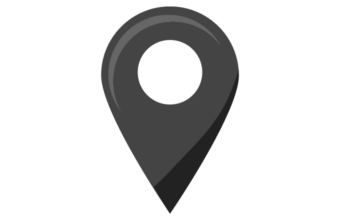
Local Supply Chain
Extensive experience in manufacturing and supplying of rapid tests, coupled with local procurement, distribution, and storage, leads to shorter lead times, and a smaller environmental footprint
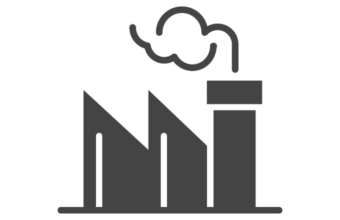
Produced in Africa
Assay and buffer manufacturing, as well as assembly, are conducted in Cape Town, South Africa
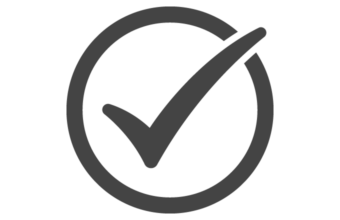
Quality Management System
All processes are validated and verified with batch release testing for every production
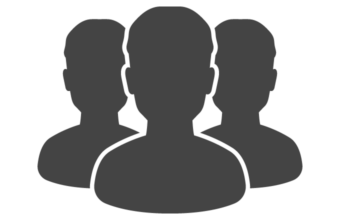
Experienced & Skilled Staff
We create local employment opportunities in South Africa while providing ongoing support from our regulatory and engineering teams
Manufacturing Automation
Atomo has developed proprietary blister technology specifically designed for our Pascal and Elion cassettes, offering significant advantages. The blister technology features an integrated buffer delivery system that ensures a precise, metered amount of fluid is delivered with each use, thereby reducing the quantity of fluid required per test and enhancing the overall usability of the tests. Each blister is composed of top and bottom webbing that encases the fluid within a well, sealed with a frangible seal. Atomo’s fully automated blister machine, located near our Leichhardt headquarters, is capable of producing nearly 50,000 blisters per day. Additionally, Atomo can create custom blister solutions tailored to the specific needs of organisations.
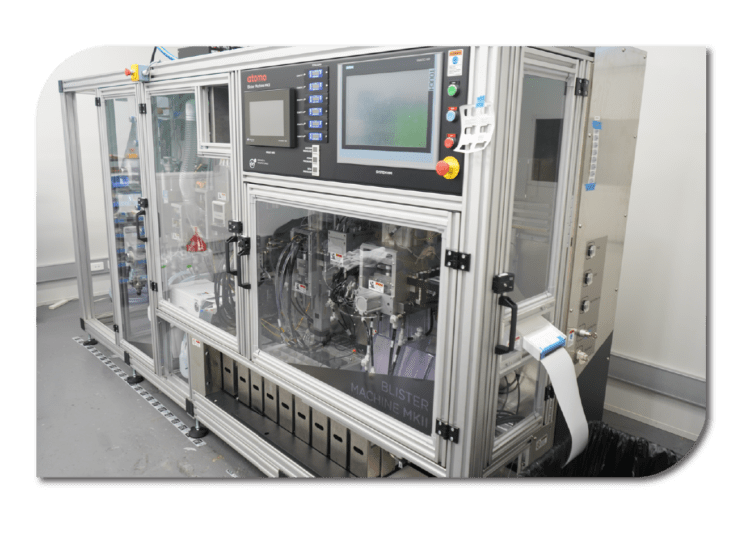
Environmental Sustainability
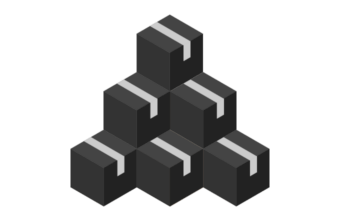
Packaging Optimisation
Optimising the packaging tray allows for 33.3% more devices per box, resulting in a 33% cost reduction and an estimated 25% decrease in CO2 emissions
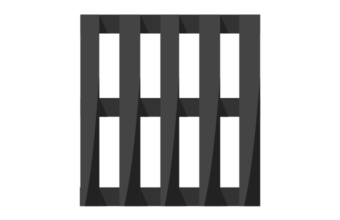
Recyclable Pallets
The use of recyclable pallets has led to a 55% cost reduction, an estimated 933 kg decrease in CO2 emissions, and approximately 100 tons of trees saved.